鋁合金產(chǎn)品加工易產(chǎn)生的9中誤差
發(fā)布時(shí)間: 2019.11.28 瀏覽次數(shù):
鋁合金產(chǎn)品加工的時(shí)候?qū)纫蠓浅5母撸卿X合金產(chǎn)品加工中難免會(huì)出現(xiàn)一些誤差,那么鋁合金產(chǎn)品加工都有哪些誤差呢?下面我們就一起來(lái)了解一下吧! 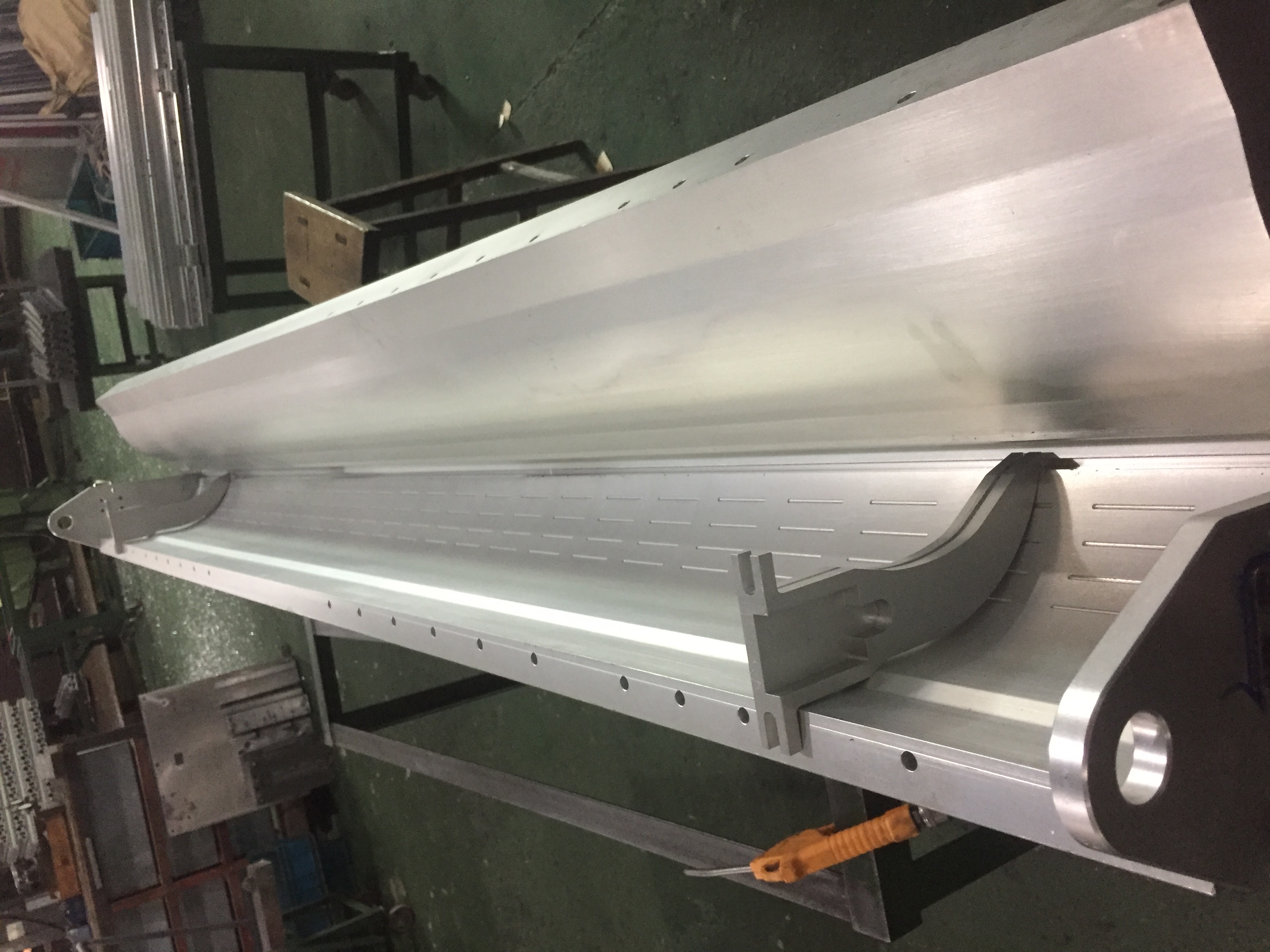
鋁型材加工后實(shí)際幾何參數(shù)與理想幾何參數(shù)的吻合程度是鋁型材的加工精度。加工誤差越小,符合度越高,加工精度越高。鋁型材的加工精度和加工誤差是一個(gè)問(wèn)題的兩個(gè)方面?! ′X型材加工誤差的主要原因 一是機(jī)床制造誤差 機(jī)床制造誤差主要包括主軸回轉(zhuǎn)誤差、導(dǎo)軌誤差和傳動(dòng)鏈誤差?! 《菉A具引起的誤差 在鋁型材加工中,夾具的作用是使工件等效于刀具和機(jī)床的正確位置,因此夾具的幾何誤差對(duì)加工誤差(尤其是位置誤差)有很大的影響?! 〉谌晒ぞ咭鸬恼`差 任何刀具在切割過(guò)程中都會(huì)不可避免地磨損,從而導(dǎo)致鋁型材的尺寸和形狀發(fā)生變化。刀具幾何誤差對(duì)加工誤差的影響因刀具類(lèi)型的不同而有所不同:當(dāng)使用固定尺寸刀具加工時(shí),刀具的加工誤差將直接影響鋁型材零件的加工精度;對(duì)于一般刀具(如車(chē)刀),加工誤差對(duì)加工誤差沒(méi)有直接影響?! ∷氖嵌ㄎ徽`差 定位誤差主要包括基準(zhǔn)定位誤差和定位分制造誤差。在機(jī)床上加工鋁型材時(shí),必須選擇工件上的幾個(gè)幾何要素作為加工的定位基準(zhǔn)。如果使用選定的定位基準(zhǔn)和設(shè)計(jì)依據(jù)(使用零件尺寸來(lái)確定表面的尺寸和位置)。基準(zhǔn)測(cè)試)不一致,導(dǎo)致基線不匹配錯(cuò)誤?! ′X型材零件的定位面與夾具定位元件一起構(gòu)成定位副。由于定位副的制造不準(zhǔn)確以及定位副之間的匹配間隙導(dǎo)致工件的大位置變化,稱(chēng)為定位誤差制造誤差。定位誤差和制造誤差只有在使用調(diào)整方法時(shí)才會(huì)產(chǎn)生,不會(huì)在試切過(guò)程中發(fā)生?! ∥迨枪に囅到y(tǒng)熱變形 加工系統(tǒng)的熱變形對(duì)加工誤差有很大的影響。特別是在精密加工和長(zhǎng)材料加工中,由熱變形引起的加工誤差有時(shí)可占到工件總誤差的50%?! ×枪に囅到y(tǒng)受力變形 工件剛度:在加工系統(tǒng)中,如果工件剛度相對(duì)于機(jī)床、刀具、夾具較低,在切削力的作用下,由于鋁型材剛度不足引起的變形對(duì)加工誤差影響較大。 刀具剛度:外圓車(chē)刀在被加工表面法向(y)方向的剛度非常大,其變形可以忽略不計(jì)。內(nèi)的內(nèi)部直徑較小的直徑,桿的剛度很差,和桿的變形有很大的影響在孔的加工精度。 機(jī)床部件剛度:機(jī)床部件由多個(gè)部件組成。機(jī)床構(gòu)件剛度沒(méi)有合適的簡(jiǎn)單計(jì)算方法。目前,實(shí)驗(yàn)方法主要用于確定機(jī)床構(gòu)件剛度。影響機(jī)床零件剛度的因素有:接頭接觸變形的影響、摩擦力的影響、低剛度零件的影響、間隙的影響。 7、調(diào)整誤差 在鋁型材加工的各個(gè)過(guò)程中,工藝系統(tǒng)總是以這樣或那樣的方式進(jìn)行調(diào)整。由于調(diào)整不可能絕對(duì)準(zhǔn)確,因此會(huì)產(chǎn)生調(diào)整誤差。在加工系統(tǒng)中,通過(guò)調(diào)整機(jī)床、刀具、夾具或工件來(lái)保證工件與刀具在機(jī)床上的相互定位精度。當(dāng)機(jī)床、刀具、夾具、鋁件毛坯的原始精度滿足工藝要求而不考慮動(dòng)態(tài)因素時(shí),調(diào)整誤差對(duì)加工誤差起決定性作用。 八、測(cè)量誤差 當(dāng)零件在加工過(guò)程中或加工后被測(cè)量時(shí),測(cè)量方法、量具的精度、工件的精度以及主客觀因素直接影響測(cè)量的精度?! 【?、內(nèi)部壓力 鋁型材零件內(nèi)部存在的應(yīng)力。
通過(guò)上面鋁合金產(chǎn)品加工廠家的介紹大家應(yīng)該知道鋁合金產(chǎn)品加工易產(chǎn)生的誤差有哪些了吧!
更多鋁合金產(chǎn)品加工相關(guān)資訊請(qǐng)?jiān)L問(wèn)官網(wǎng):http://m.mdbusinesssolutionsllc.com/